Most people’s first introduction to safety cans is at home. Those red plastic jugs- usually known as gas cans or safety gas cans- are ubiquitous in garages, basements, and (though it’s not recommended) car trunks everywhere. For the layperson, they’re often more of a nuisance than anything else- they spill easily, spread fumes, are a pain to refill- and they can explode if they’re not stored properly.
But safety cans come in a lot more shapes, colors, and sizes than those aforementioned fire engine red staples, and they’re an essential tool for many of the biggest industries in the world-from Automotive and Healthcare to Manufacturing and Construction. The materials they’re built with, their basic design, and their additional safety features vary depending on their intended use. Whether you are managing a garage, laboratory, warehouse or plant, being familiar with safety cans is essential for running a safe, productive, and efficient operation.
SAFETY CAN SAFETY
Proper storage and use of explosive and flammable petrochemicals, toxic or corrosive liquids, or biohazardous materials is a matter of life or death for both workers and businesses themselves.
The complexities of litigation, disclosure agreements, and sometimes record-keeping malfeasance make statistics on industrial workplace death and injury murky, but for decades, safety can-related incidents were a serious enough issue that agencies like OSHA and the NFPA have imposed strict regulations on the design of commercial safety cans- leading to safer workplaces in recent years.
Commercial safety cans are used for the storage and dispensation of petrochemicals, caustic and toxic solutions, and biohazardous materials, all of which require different designs and materials.
There are two basic types of safety cans available for industrial use- Type 1 and Type 2. What is the difference between a Type 1 and Type 2 Safety Can?
TYPE 1
Type 1 Safety Cans have a maximum capacity of five gallons, and have only one opening, used for both pouring and filling. Nearly anything called a gas can is a Type 1 safety can.
Type 1 safety cans are also available in several subtypes:
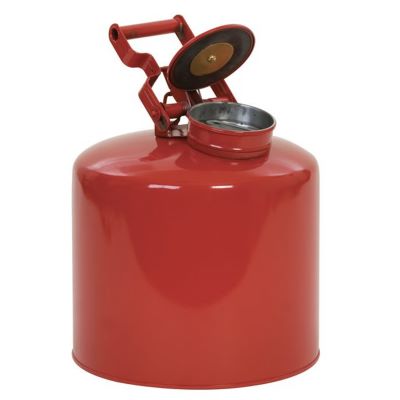
DISPOSAL CANS
Disposal Cans, also common in healthcare as well as manufacturing for the disposal of biohazardous, toxic, or caustic chemicals, and are designed to prevent dangerous vapors from escaping containment before disposal.
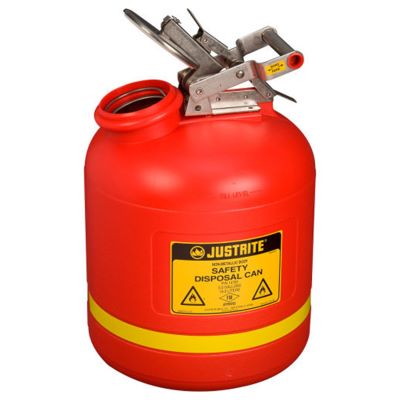
OILY WASTE CANS
Oily Waste Cans, used for the disposal of solvent and petrochemical waste-soaked rags, common in many industries.
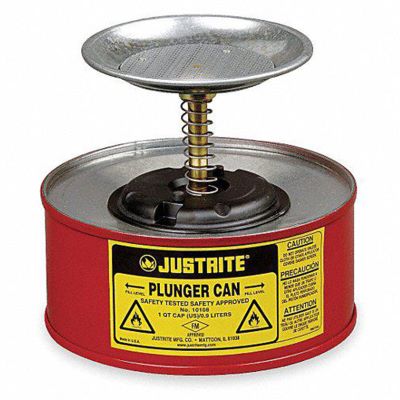
BENCH AND PLUNGER CANS
Bench and Plunger cans, used in various industries including healthcare and construction, designed, like disposal cans, to control the release of vapors and free liquids during cleaning
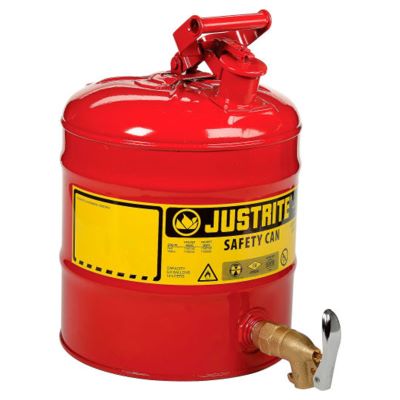
FAUCET CANS
Faucet Cans, designed for a more controlled pouring of fuels and solvents, also common in many industries
TYPE 2
Type 2 safety cans are defined by having two openings- one for pouring and one for filling, and are more commonly used for flammable materials to help prevent flashback- where a flame moves “upstream” back into a hose, spout, or dispenser, potentially causing a dangerous explosion. As such, they’re more commonly found in auto shops and petrochemical facilities than in healthcare and construction. The variation amongst Type 2 cans comes primarily from the materials they’re built with.
COLOR CODING
What do the different colors of gas cans mean?
Color coding in safety cans is primarily used in petrochemical storage and use- as such they’re common in the automotive industry but can be found in manufacturing and construction to a lesser extent.
Industry-standard brands like Justrite and Eagle Safety Cans use a simple system to ensure fuel types are stored correctly and aren’t accidentally mixed- red for gasoline, yellow for diesel, blue for kerosene, and green for oil.
Materials
Safety cans can be built using a variety of materials, depending on their intended purpose. Some are more cost-effective and lighter than others, while some are more durable and more rust and corrosion-resistant, making them more suitable for heavy-duty manufacturing.
Steel
Steel is the most common material used to make safety cans because of its heat resistance, durability, and relative ease of manufacture. As such, they’re common in construction and manufacturing, and less common in healthcare.
Their flame and heat resistance makes them a mainstay of auto shops and petrochemical facilities, where the need to safely handle volatile, or highly inflammable materials is paramount. Frequently, steel cans are made with a powder-coat finish to help prevent rusting. There are two different main variants of steel cans, each with its special properties:
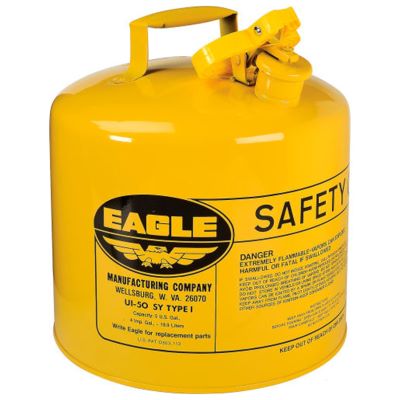
GALVANIZED STEEL SAFETY CANS
Galvanized Steel safety cans have a layer of zinc coating to make them more corrosion-resistant and are commonly found on construction sites where flammable liquids need safe storage.
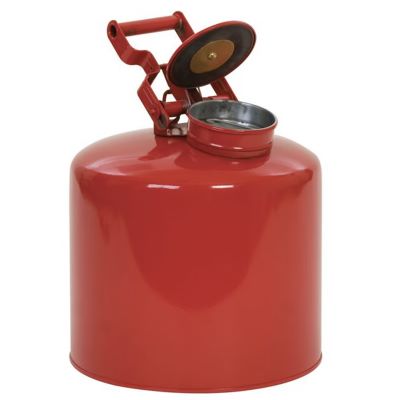
STAINLESS STEEL SAFETY CANS
Stainless Steel safety cans offer additional protection from corrosion and are popular in industrial settings for heavy-duty storing of corrosive and highly reactive or explosive chemicals.
High-Density Polyethylene
High-Density Polyethylene or HDPE is a high-tech plastic sought after for being ultra-lightweight and relatively durable and corrosion-resistant- for a plastic. While safety cans made with HDPE aren’t as impact-resistant or chemical-resistant as steel, they still offer a good amount of corrosion protection and durability while being significantly lighter and more cost-effective.
Polypropylene
(PP) is another plastic that offers some degree of chemical resistance and is lighter and even less pricey than HDPE. It’s not nearly as durable as steel or even HDPE and it’s not suitable for the most corrosive chemicals, especially for long-term storage, but for shops and facilities on a budget that aren’t working with ultra-corrosive or dangerous chemicals, it’s a more cost-effective option than either Steel or HDPE.
Fiberglass
Fiberglass- made by embedding glass fibers into a high-tech resin- is a popular choice in some industries due to its high corrosion resistance, low weight, and, crucially, the fact that it does not conduct electricity.
Fiberglass can be a good choice for manufacturing sites and workshops with open electricity exposure that also use corrosive, flammable, and reactive chemicals, however, some studies warn about the possible carcinogenic properties of fiberglass material, showing that frequent and long-term unprotected exposure to them can lead to respiratory and other illnesses and complications. Sites with poor ventilation and low ceilings may want to consider this fact before investing in fiberglass storage in general.
Aluminum
Aluminum safety cans are popular in the automotive and aerospace industries for their excellent (though still inferior to steel) corrosion resistance and lightweight- though most plastics are still lighter. They’re somewhat of a middle ground between the cost-effectiveness and lower weight of plastics and the durability of steel. However, they can explode when introduced to extreme heat, making them less suitable for heavy manufacturing.
Safety Features
Beyond their basic design, most safety cans come with a variety of safety features to further comply with industry and federal standards.
1. Flashback Arrestors
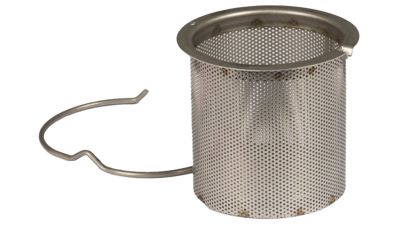
Flashback is the phenomenon where a flame burns back into a gas supply line, causing a dangerous explosion. Flashback arrestors- which are common in safety cans of all kinds- generally work with an arrestor screen inside the spout which automatically closes when not pouring. Justrite Safety Cans, for example, get the job done using an ultra-effective double mesh arrestor screen.
When shopping for 5 gallon safety gas cans, this is the first feature you should look for, as flashback can occur in many different scenarios, even when an open flame is not involved. OSHA does not require flashback arrestors to be installed in safety cans, but it has cited general failure to follow safety guidelines in accidents, including the lack of arrestor screens.
Flashback arrestors aren’t commonly found in healthcare, where open flames, electricity, and flammable materials aren’t typically an issue, but they’re used widely in manufacturing and construction, and are an absolute necessity in auto shops and similar facilities.
2. Spring-Loaded/Self-Closing Lid
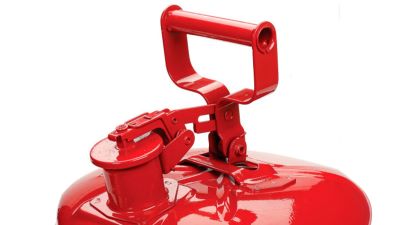
OSHA regulations require all safety cans to come built with a spring-loaded or otherwise self-closing lid. A self-closing lid or cap allows for a leak-proof seal at the edges of the spout, preventing spills and further protecting chemicals from heat sources and preventing flammable or toxic vapors from escaping. This is therefore a ubiquitous feature across most safety can types and most industries.
3. Positive Pressure Release Valve
A Positive Pressure Release valve releases vapor pressure between 3-5 psi to prevent any risk of dangerous pressure build-up in a safety can. These valves, like spring-loaded and self-closing lids, are required per OSHA regulations.
Safety Regulations Per Agency
Most government regulatory agencies related to industry have special regulations for safety cans. It’s important to understand these regulations well and enforce them effectively in your own business to avoid heavy fees, fines, and other legal penalties.
OSHA and NFPA
OSHA regulations state that for a container to be called a “safety can,” it must have a maximum capacity of no more than five gallons, a spring-closing lid and spout cover to protect against ignition of flammable liquids and have a mesh flashback arrestor. The NFPA, or National Fire Protection Association, has the same requirements. OSHA approved gas cans and safety cans are more of the rule in the industrial market rather than the exception.
CARB
Carb, or the California Air Resources Board, is a state-level air pollution regulatory body established in 1967. In 2009, CARB banned the sale of traditional gas cans and started to require that all safety cans be self-closing using a spring-closing lid on all openings.
Underwriters Laboratory
Underwriters Laboratory or UL is a global nonprofit organization that works with applied safety science to test the safety of materials, equipment, devices, constructions, methods, and systems in all industries. Its primary function is to maintain a list of industrial products approved by them for safe use.
In order to receive UL certification, a safety can must:
-
Have a maximum capacity of 5.3 gallons or 20 liters
-
Have a minimum capacity of 8 fl oz or 236 milliliters
-
Is intended for storage and handling of flammable and combustible liquids.
THE RIGHT TOOL FOR THE RIGHT JOB.
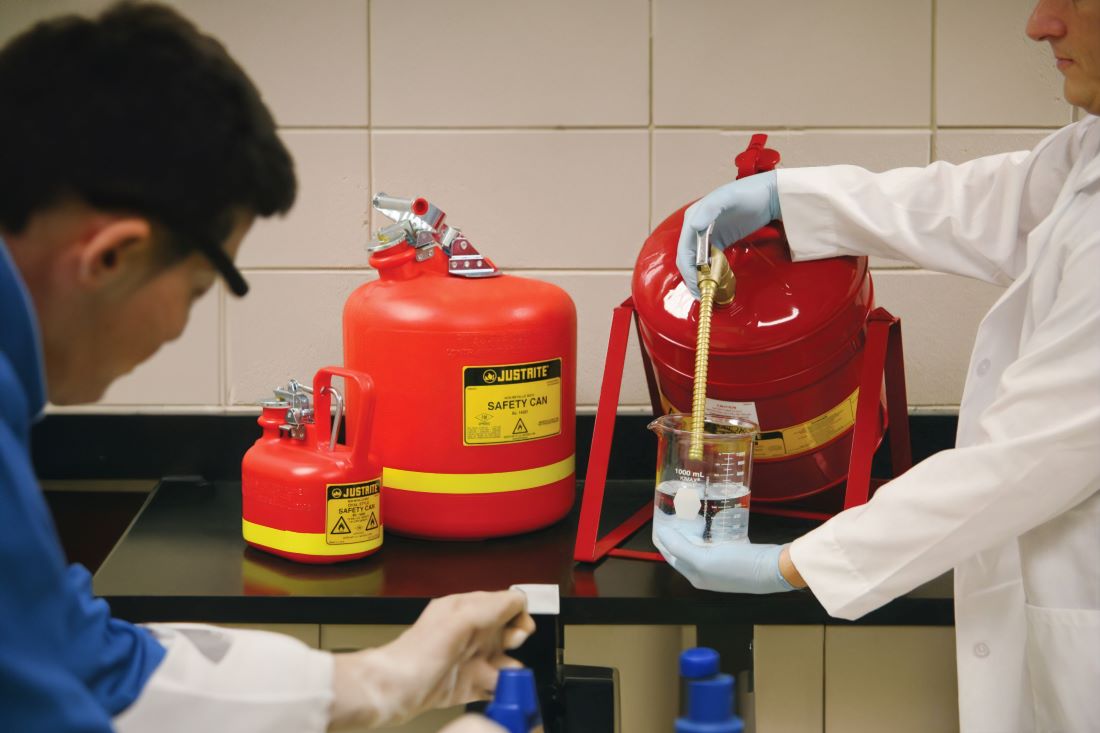
We’ve gone over the various types of safety cans and their most common uses across some major industries, but while you’ll often find some types are more common in some industries, there’s plenty of crossover, and not every workplace, shop, and laboratory have safety can type purpose-built for it. Let’s summarize the most common types of safety cans- both per design and material- for each of the three major industries in which safety cans are most often used.
Healthcare
In the Healthcare industry, safety cans are most commonly used hospitals, urgent care facilities, and research labs. The most common needs of such facilities in when it comes to chemical handling are storage and disposal and storage of caustic solvents and biohazardous materials. Type 1 steel or fiberglass safety cans are the best choice when it comes to containing highly corrosive materials, but lower-cost plastic and aluminum safety cans are a reasonable choice for non-corrosive materials. Type 2 safety cans aren’t generally necessary since flammable materials aren’t typically found in such facilities.
Manufacturing
The manufacturing industry has a wide array of needs when it comes to chemical storage and handling, since flammable, explosive, caustic, and toxic liquids are all common in manufacturing facilities, as are high temperatures, open flames and heat sources, exposed electricity, sparks, and suboptimal ventilation. Because of these factors, galvanized and stainless-steel safety cans (primarily Type 1) will be a good choice much of the time, and cost must necessarily come second as a consideration.
Construction
When it comes to safety cans, the needs of the construction industry are much the same as those of manufacturing, however, the need to fuel construction vehicles such as backhoes means a greater need for Type 2, dual-opening cans. Otherwise, steel will again be the best choice most of the time.
Safety cans are an essential part of so many industries because they’re one of the biggest ways to reduce risk. Proper storage of dangerous substances is a factor that can’t be overlooked in any commercial setting, but armed with as much information as possible, they’re the most important tool you’ll never have to think about.
The information contained in this article is for informational, educational, and promotional purposes only and is based on information available as of the initial date of publication. It is the reader’s responsibility to ensure compliance with all applicable laws, rules, codes and regulations. If there is any question or doubt in regard to any element contained in this article, please consult a licensed professional. Under no circumstances will Global Industrial® be liable for any loss or damage caused by your reliance on this article.